Plywood vs MDF vs Particleboard — it’s one of the most common debates in woodworking and DIY projects. If you’ve ever stood in the lumber aisle trying to decide which sheet to grab, you’re not alone. I’ve used all three materials in cabinet builds, furniture projects, and shop setups — and they each have their strengths and weaknesses.
In this guide, I’ll break down exactly when to use plywood, when MDF makes more sense, and why particleboard might work in some cases (but usually doesn’t). I’ll share what’s worked for me in real-world projects — no fluff, just honest comparisons.
🧱 How I Read a Plywood Label (Without Guessing)
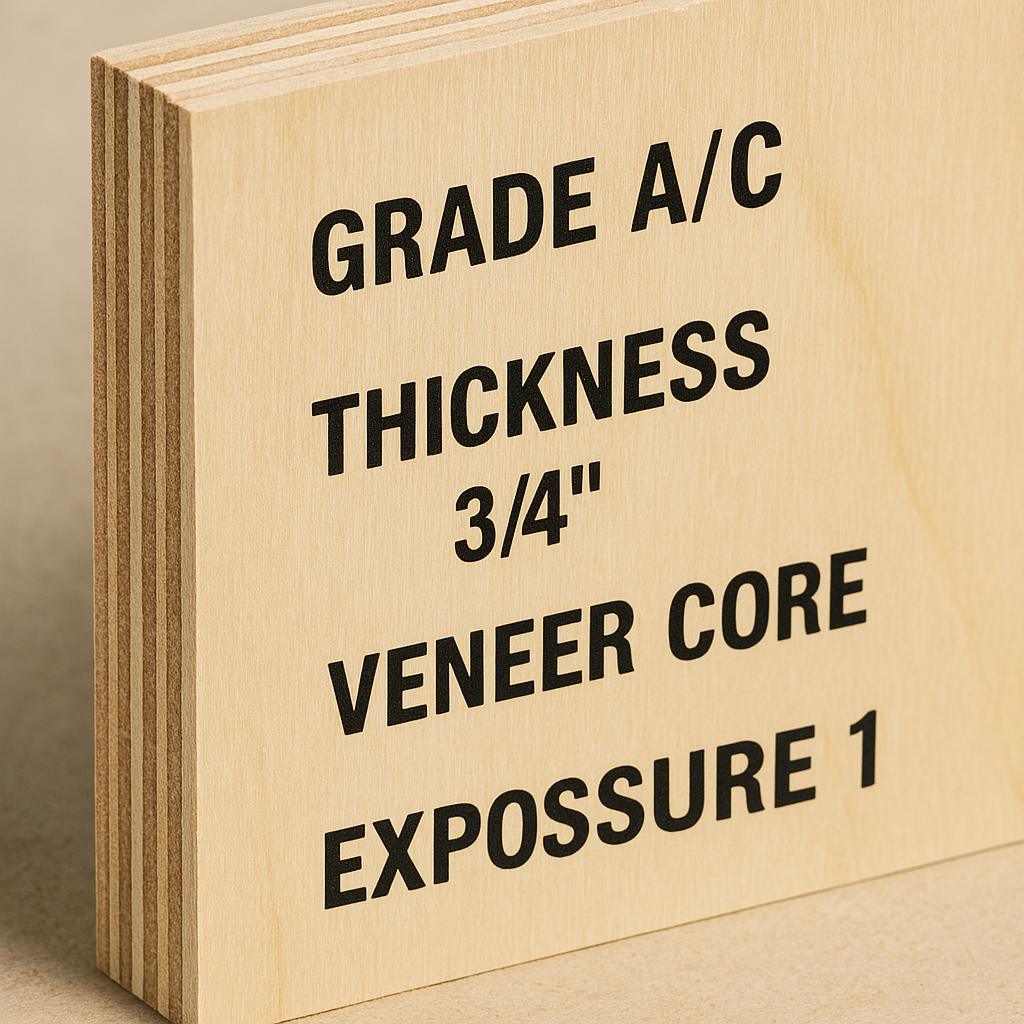
Shopping for plywood used to make me feel like I needed a decoder ring. Sometimes the grade’s printed right on the face. Other times, you’re stuck peeling off a half-torn sticker and squinting at faint stenciled ink.
Here’s how I handle it now:
1. Grade Code (A/C, B/BB, etc.)
This tells you the face and back veneer quality — the first letter is always the “good” side. If it’s A/C, the face is decent, and the back… not so much. For Baltic birch or ApplePly, you’ll see Euro grades like B/BB.
2. Thickness
Almost nothing is exactly what it says. “3/4-inch” plywood usually measures 23/32″, and 1/2″ is often closer to 15/32″. If you’re cutting dados or using a router bit, don’t trust the label — measure it.
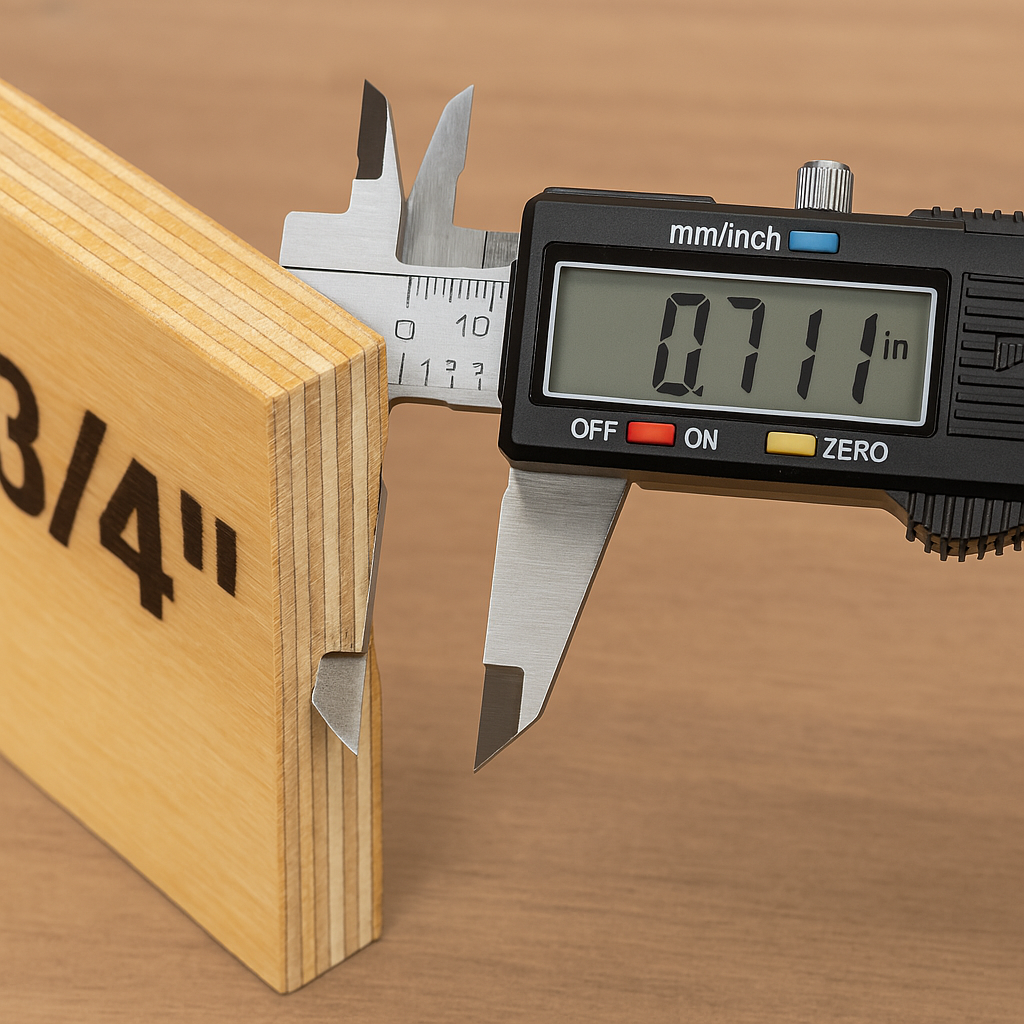
🛠️ Lesson learned: I once made a cabinet carcass where none of the shelves fit their dados. Why? I routed them to 3/4″ and the plywood was thinner. Rookie mistake.
3. Core Type
You won’t always see this on the tag, so flip the sheet and check the edge. If it looks like stacked layers of pancakes, it’s a veneer core. If it looks like dusty cereal bars? That’s MDF or particleboard.
4. Glue Type
If you see “Exposure 1” or “Exterior,” that means it’s moisture-resistant. CDX often has this. Most interior plywood is fine for cabinets, but if it’s for a bathroom or basement, spring for exterior glue.
🧰 Tools That Make Plywood Work Way Easier
I used to manhandle full sheets across a table saw solo, and let me tell you — it’s not worth it. These days, I use tools that actually make the job go smoother and safer.
✅ Track Saw or Circular Saw + Guide
I picked up a Makita track saw a few years back and haven’t looked back. I can break down 4×8 sheets solo, no drama, no tear-out.
✅ 80T or 100T Blades
For circular saws or table saws, go with fine-tooth. I use a Diablo 80T on plywood and it cuts like butter without destroying the veneer.
✅ Painter’s Tape Trick
Slap some blue tape down where you’re cutting — reduces splintering on cheap plywood or anything with a thin face veneer.
✅ Kreg Pocket Hole Jig
If you’re building face frames, drawers, or even just quick shop shelves, this jig is a total game-changer. Clean joints; no fancy clamps are needed.
❌ Common Plywood Mistakes (I’ve Made ‘Em All)
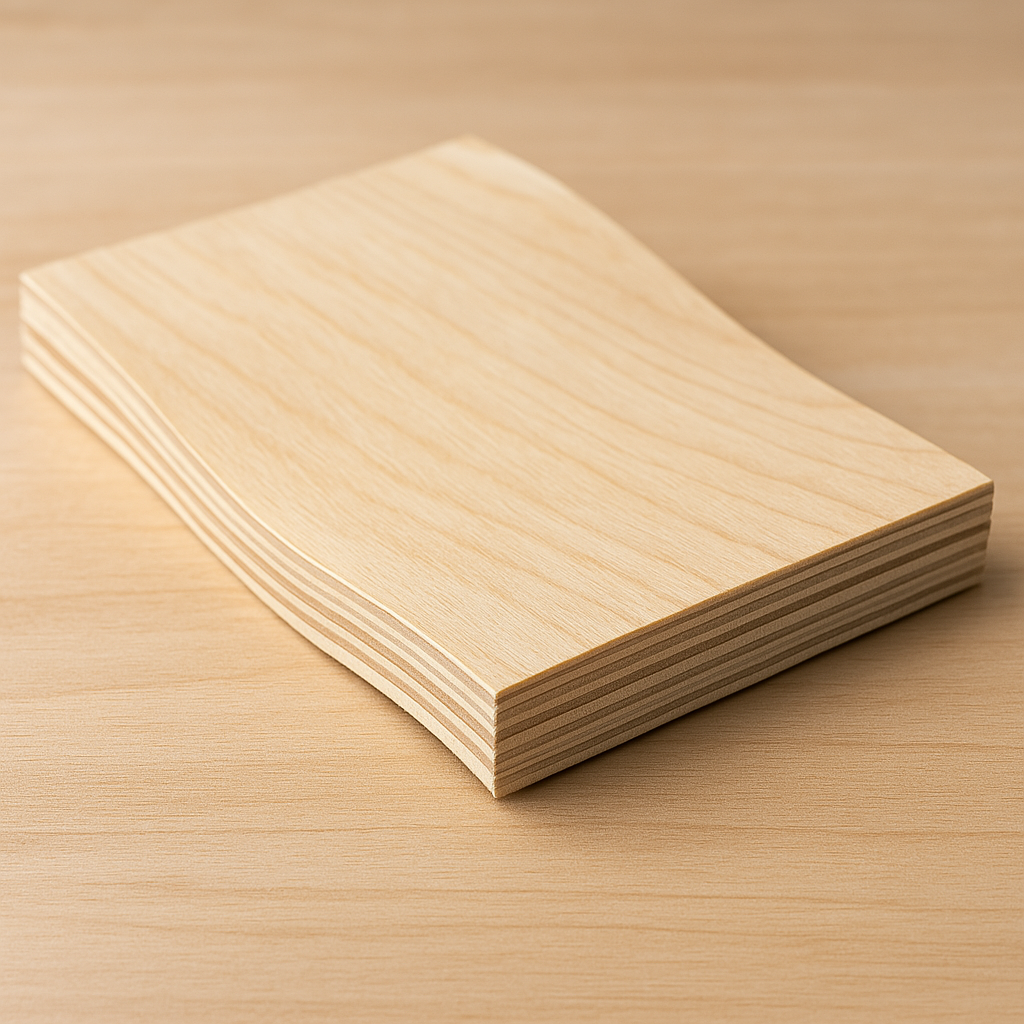
Let me save you some time and frustration. These are the things I learned the hard way — usually late at night before a deadline.
1. Using Cheap Sheets on a “Nice” Project
Don’t do it. Even if you save $25 a sheet, you’ll spend more in filler, sanding, cursing, and wasted cuts.
2. Not Checking the Back Side
The face might look great, but if the back is warped or full of patches, that panel’s not gonna lay flat or glue up well.
3. Skipping Acclimation
If the plywood’s been sitting in a cold truck or hot garage, give it a couple of days in your shop to adjust. Otherwise, it might shift or warp after you cut.
4. Only Finishing One Side
I did this once on some garage cabinets, and within a week, the doors started cupping. Now, I always finish both sides — even if it’s just a quick coat of clear poly.
5. Overtightening Screws at the Edges
Especially with MDF core, you’ll split the edge or blow through the face veneer. Pilot holes and a light hand go a long way.
🧱 MDF (Medium-Density Fiberboard)

- Strength: Decent in compression, poor with fasteners unless pre-drilled.
- Durability: Chips easily, especially at corners. Doesn’t like moisture.
- Weight: Heavy — very heavy, especially in 3/4″ thickness.
- Finish: Takes paint incredibly well — smooth, no visible grain. But stains? Not so much.
Use MDF for:
Painted cabinet doors, wainscoting, built-ins, or panels that won’t see much wear.
🧠 Pro tip: MDF can be great for speaker boxes or shop fixtures — just keep it dry. I had a jig made from MDF fall apart after a minor spill. Lesson learned.
🌽 Particleboard

- Strength: The weakest of the bunch. Sags quickly under weight.
- Durability: Poor. Chips, swells with moisture, and can crumble if mishandled.
- Weight: Similar to MDF, maybe a touch lighter.
- Finish: Usually covered in laminate or melamine. Doesn’t hold screws well.
Use particleboard for:
Nothing structural. It’s okay for inexpensive furniture or cabinets where it’s fully supported and never moves — think office desks or cheap flat-pack drawers.
🔍 Why I Choose Plywood 9 Times Out of 10
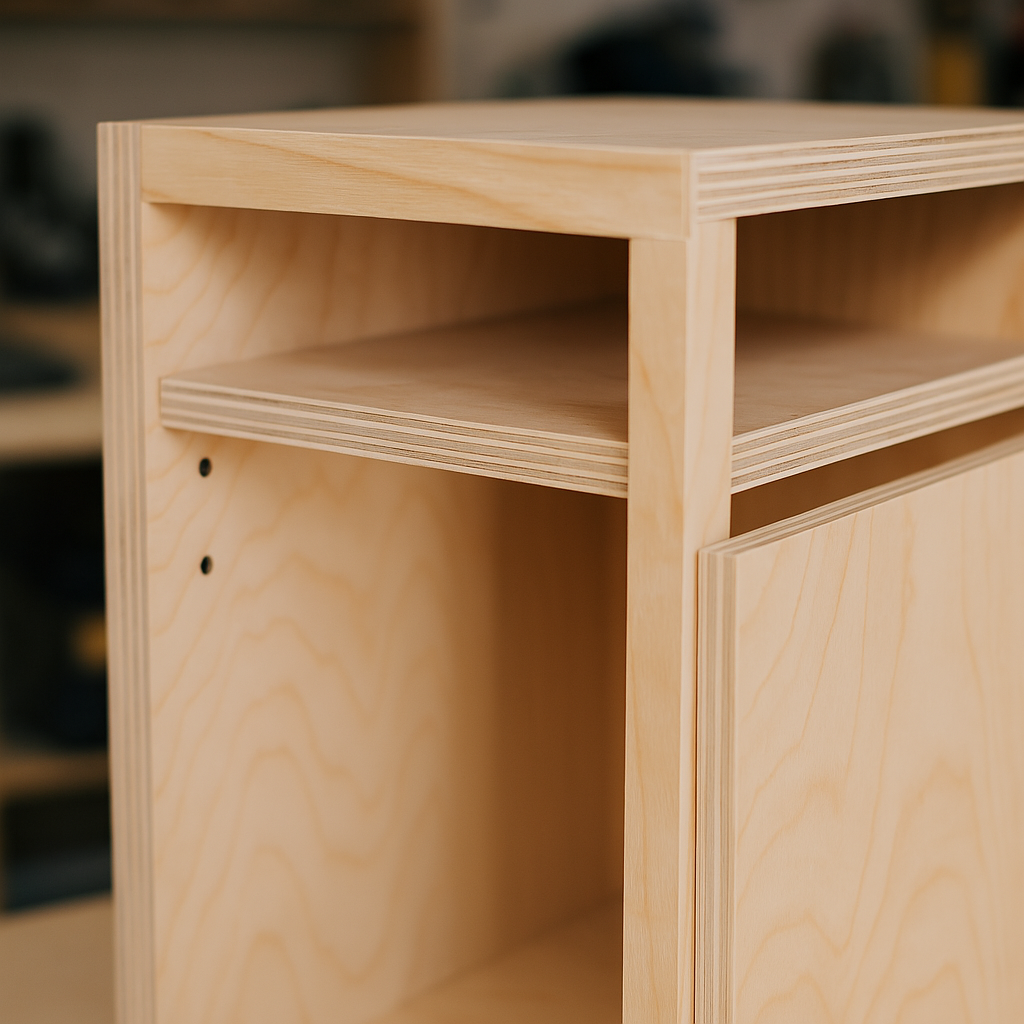
I’ve built with all three. In the short term, MDF and particleboard might seem “good enough,” especially if you’re on a budget. But when I return to a project 6 months later and the drawers are sagging or the fasteners are pulling out of crumbly cores, it’s a reminder that plywood is worth the extra cost.
Plywood handles weight, movement, moisture, and fasteners better. And if you’re taking the time to build something yourself, you probably want it to last. That’s why, for cabinets, shelves, or just about anything that’s not decorative trim — I go plywood every time.
🪚 Real Talk: What the Right Grade Gets You
At the end of the day, plywood grading is more than a label — it’s about knowing what to expect and planning your project around it.
If I’m building something for the house — a cabinet, bookshelf, vanity — I want plywood that’s flat, clean, and dependable. That’s usually Baltic birch or a decent maple veneer sheet. But if I’m making a shop jig or building out storage in the garage? I’ll gladly grab the cheaper C-grade or CDX.
The key is to know what you’re building and match the material to the job.
Related: Best Plywood for Cabinets (From My Workshop to Yours)
Also read: Types of Plywood and Their Uses