Plywood is a suitable choice for subfloors in all types of environments. It can be used as a subfloor for bathrooms, bedrooms, attics, sheds, basements, and garages. While most plywood can withstand slight moisture, damp environments, and rainfall, it should not be left exposed to water for long periods without protection.
Getting plywood wet can be unavoidable, particularly when building an outdoor construction, like a shed, or dealing with an interior leak. Subfloors can be dried and moisture removed, provided the right conditions are created. Generally, a plywood subfloor will not be ruined after suitably drying it, but slight warping can occur with excessive moisture.
Keep reading to learn how to get moisture out of plywood subfloor indoors and outdoors.
Will Wet Subfloor Dry Out?
In short, yes, a wet subfloor will dry out, but only when the right conditions are created to dry wet plywood. For example, if you increase the temperature of the room and reduce the humidity. Or by leaving planks in the sunlight, raised off the ground, and flipping the planks routinely.
However, wet wood floors won’t usually dry out on their own. This is particularly the case if it’s left in the same conditions that caused the moisture or if it’s left in a cool, damp environment, like a basement, shed, or garage. How long plywood takes to dry depends on how wet it is, but it shouldn’t take more than a week.
When plywood subfloor gets wet from minor rainfall or a leak, it should still be suitable for continued use. Plywood can warp when it becomes very wet, but this is unlikely to happen if the subfloor is tightly fitted together with nails or screws. However, it can become slightly warped on the edges when it dries.
If this happens, the plywood can be nailed in place to flatten the upturned corners. This should not be done if areas of the plywood have started to bow due to moisture damage. The affected areas should be cut out and replaced.
What is the Best Way to Dry Out a Subfloor?
Most subfloors are made from plywood planks. All types of plywood have a degree of moisture resistance, with some sheets, like WBP plywood (water-boiled proof) and Marine Grade plywood, being the most waterproof.
However, no plywood or subfloor should be submerged in water, left in standing water, or exposed to excessive moisture for long periods. This is the case unless it is treated with epoxy or polyurethane, or another waterproof solution. Prolonged exposure will cause warped plywood.
It’s possible to flatten warped plywood, but only if the damage has not split the core veneer layers. The best way to dry out a subfloor made from plywood is to increase the temperature and airflow of the environment while lowering the humidity.
This can be done indoors by turning on the heating and opening a window or using a dehumidifier. Drying plywood outdoors can be more difficult, particularly during bad weather. It’s best to focus efforts to prevent subfloors from water during construction, rather than fix the issues after exposure.
How to Reduce Moisture in a Subfloor Indoors
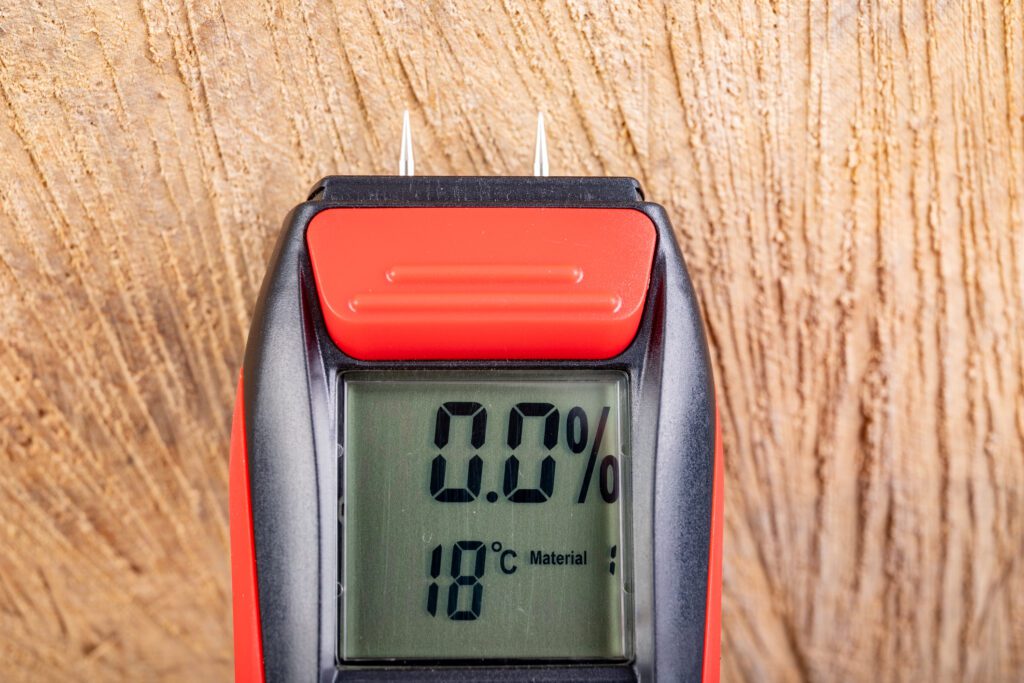
Moisture in an indoor subfloor is usually caused by a water leak or other major spillage. Minor leaks shouldn’t cause any long-term damage to a plywood subfloor. However, it’s important to clean away spills quickly and dry the wood as fast as possible.
Otherwise, the moisture can spread to other parts of the subfloor and underneath it onto the joists. This can cause dry rot, which spreads fast and can cause severe damage to the structural integrity of a property.
Indoor subfloors can usually dry out in a couple of days, depending on how severe the leak is. It’s best to wait until the floor has dried fully before applying any sealant (like a self-leveling compound) or installing a finished floor (like tiles, laminate, hardwood floors, or carpet).
To ensure the floors have dried right into the core layers, it’s best to wait a week before continuing any new construction work. This ensures the sheets are fully dried. Use a moisture meter to check the moisture content of the flooring and confirm the sheets are suitable for use.
If work continues before it’s completely dry, the moisture problem will remain under the surface. Such water damage can cause damp conditions between the subfloor and the floor joists, leading to mold growing.
Here’s how to reduce moisture in a subfloor indoors step-by-step.
1. Mop Up Excess Water
Excess water on the surface needs to be removed from the subfloor before starting the drying process. Use a mop to clean away puddles. Dry any remaining moisture with a clean cloth as best as possible. The more moisture you can remove, the faster the subfloor will dry.
2. Increase Temperatures
The best way to dry wet subfloors inside the house is to increase the surrounding temperatures. Turn the heating on in the room up to 68°F or 20°C and above. Open the window or turn on a dehumidifier in the room to reduce moisture in the air.
Don’t dry subfloors without opening a window or having a dehumidifier switched on. As the moisture in the subfloor evaporates, the water will have nowhere to go except in the air and back into the plywood subfloor. This will take the subfloor longer to dry. The prolonged moist conditions can also cause wood rot under the surface.
3. Boost Airflow Under the Subfloor
Severe leaks that have soaked the plywood subfloor need to be dried fully to prevent dry rot and mold growth. Dry rot is formed when wet wood is left in moist, cool, and damp conditions for prolonged periods. It can be destructive to a property if left to spread.
If possible, try to boost the airflow underneath the subfloor during drying. This can be done by removing a plank, allowing the warm temperatures to reach the underside of the planks to dry them out. Plywood planks can be easily reattached to a subfloor using nails or screws.
How to Get Moisture Out of Subfloor Outdoors
Drying a subfloor outdoors that’s been heavily rained on can be tricky, particularly if the weather doesn’t ease up. If the rainfall was unexpected and the forecast for the next week is warm and sunny, the subfloor should be left to dry naturally.
If the floor is nailed down, consider removing one or two planks across the subfloor. This will allow airflow under the floor, helping it dry faster. It will also prevent humidity under the surface, particularly during very hot weather, which can cause mold spores.
If rainfall is expected to continue for several days or weeks, the plywood should not be left out in the rain if untreated. WBP plywood, Marine Grade plywood, or pressure-treated plywood are the most water-resistant. They can withstand long exposure to rainfall compared with other types of plywood, like OSB (Oriented Strand Board) or particle board.
Instead, the plywood sheets should be taken inside or covered until the weather improves. Dismantling the panels and keeping them in a warm, low-humidity environment raised off the ground is the fastest way to dry plywood indoors.
How Do You Protect a Subfloor During Construction?
Prevention is always easier than treatment, especially when working with a subfloor. Getting moisture out of a plywood subfloor during construction can take time and delay a project. It can also cause damage to a subfloor, like warping, bowing, and splitting of the core veneers, making it unusable.
To protect a subfloor from rainfall during construction, it should be covered when not being worked on, like overnight and during the early hours (when moisture is in the air).
Subfloors can be covered with suitably sized rosin paper or fan fold insulation with Luann on top. The seams should then be taped to the walls or unexposed ends with waterproof tape to prevent water from seeping in around the edges.
Protecting an indoor subfloor during a build project is easier than outdoors, as the conditions are more easily controlled. Exposed subfloors in bathrooms, garages, and basements need more protection than subfloors in other parts of a house. This is because these areas of the home experience high humidity.
To prevent moisture from getting to an indoor subfloor during a construction project, keep a dehumidifier in the room when the heating is on or a window open. This is particularly important if bathrooms are still in use and/or a non-waterproof type of plywood is used.
Summary
Subfloors are prone to getting wet during construction projects or in everyday life. For example, if it rains while building an external structure or if a leak is experienced while the subfloors are exposed.
When a moisture problem occurs in subfloors, it’s important to act quickly to avoid compromising the structural integrity of the boards. When this happens, you’ll need to cut out the affected areas and replace them with new plywood sheets.
Before continuing construction on a subfloor or laying flooring, use a moisture meter to measure the moisture content of the boards. If the boards are still wet, allow longer for them to dry.
Most subfloors can dry in a couple of days in the right environment, but up to a week is usually necessary to ensure plywood sheets are fully dry.