When people speak of eucalyptus, they most often think of its medicinal properties. Eucalyptus oil has been long used to treat nasal congestion and asthma, as well as for a tick repellant. It is also used as a herbal remedy for arthritis and skin ulcers.
Yet the wood of the eucalyptus tree has been largely ignored. This beautiful wood looks similar to teak, although its color can vary, from a more reddish hue to the color of sand. Eucalyptus wood has been successfully used as a replacement for teak in both outdoor furniture and hardwood flooring. Yet its acceptance by the woodworking industry has been slow.
Much of the reluctance to use eucalyptus wood and plywood has been due to the difficulties of drying the wood. When harvested, eucalyptus has a very high moisture content, making it so that the wood warps, twists and cracks easily when drying. Drying must be undertaken as soon as the wood has dried. If it is not dried correctly, much of the wood is rendered unusable for construction, furniture and other woodworking uses. However, a new method of cutting, developed by the Dehra Dun-based Forest Research Institute has developed a new method of “radial sawing” which yields a much higher rate of usable lumber from eucalyptus logs.
Eucalyptus is not a single type of tree, but rather a family of over 700 types of trees and buses, growing primarily in Australia. It was imported from there to the United States in the 1850s, where it was planted in California in anticipation of a lumber shortage that never happened. The various types of eucalyptus trees grow rapidly, making it a very sustainable wood to use.
Most eucalyptus plywood is manufactured in China, where the tree is grown on large plantations. Trees can be harvested in as little as 35 years, much faster than many other hardwoods. With the recent advancements in methods for cutting the wood, this makes it a good substitute for replacing poplar as a material for making up the core plies in hardwood plywood. Eucalyptus plywood may be finished in a variety of ways, with other hardwoods providing the face and back veneers, while the core is made of eucalyptus wood. When compared to plywood made with a poplar core, eucalyptus core plywood is darker and slightly heavier. The higher density of the wood makes for stronger plywood.
Eucalyptus wood is also made into hardboard, which is available through Home Depot. The higher density of the wood works well for tempered boards, creating a highly durable product. Natural oils in the wood help it to resist decay and insects. The wood is naturally water resistant and will not become damaged if wet.
While eucalyptus is a strong wood, it tends to be a bit on the brittle side, with low shock resistance. It also has a tendency to expand and contract more extremely than other types of wood, from changes in the moisture and temperature. Eucalyptus is not a good wood choice for cold climates, especially for outdoor use. However, it is used extensively for outdoor applications in warmer climates. It can be found in furniture, fencing, millwork, paneling and support beams.
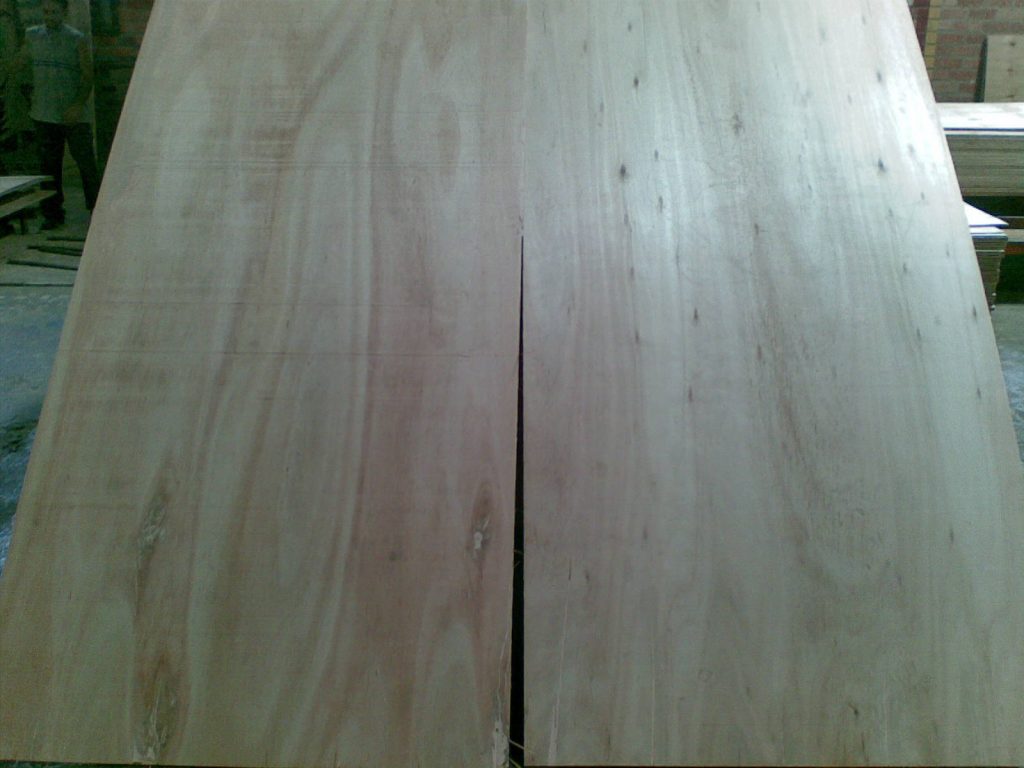
Eucalyptus wood is a popular replacement for teak in the manufacture of furniture. The greater availability and faster growth of the tree lead to lower prices, while providing a wood that is similar in appearance and durability. Properly finished outdoor furniture made from eucalyptus wood or plywood can be expected to last 25 to 30 years. However, if the wood is not properly treated, it will fade, taking on a light gray tone. Faded wood can be brought back to its original beauty by sanding and oiling it.
Eucalyptus plywood can be difficult to find in the United States. When available, it is priced comparable to domestic hardwood plywood. In most cases, the cost of shipping is more prohibitive than the cost of the plywood itself. However, eucalyptus turning blanks and slabs are readily available, some even book-matched for making fine furniture.
While eucalyptus is not difficult to mill, its sensitivity to moist should be taken into consideration when using it. Allow boards time to acclimate to the temperature and moisture level in the workshop, before using the wood to avoid shrinkage problems. Be sure to seal the cut ends of pieces well when finish projects, in order to reduce the wood’s ability to absorb moisture.