Medium Density Fiberboard (MDF) is a plywood product which is commonly used as a substitute for plywood and particleboard, for new construction, home-improvement projects and furniture building. Its low cost, smooth finish and overall strength make it a popular material to use. Building code allows for the use of MDF as a replacement for plywood in a number of applications.
First manufactured industrially in the 1980’s, MDF is composed of small wood fibers, binding resins and a small amount of paraffin wax. The wood fibers used in the production of MDF normally come from softwood sawdust/wastes, but other materials such as hardwoods, cardboard, newsprint and even old telephone books can be used as the substrate material. There are also a variety of binding resins used, which include phenolic, melamine, isocyanate and urea-formaldehyde.
The application of heat and pressure to these materials produces a mat of uniform thickness, of any thickness desired, which is then cut to size (normally 4’ x 8’ in the US; 124 x 249 cm). MDF has a higher density than both regular plywood and particleboard, as the density is controlled during the extrusion/pressing stage of production. This gives the typical sheet of MDF a density within the range of 31–62 lb/ft3 (500–1000 kg/m3).
Please note that this density is less than that of HDF (high density fiberboard), also known under the trade name “Melmite.” MDF is much more common and much more widely used than HDF. Nevertheless, some care must be taken when using it.
MDF Properties
The popularity of MDF is largely due to its properties, many of which are ideal for furniture manufacturers. It has an incredibly smooth surface so MDF can take paint much better than real wood and is also an excellent substrate laminates and wood veneer. It is economic from both a financial and environmental standpoint; it costs less than plywood and much less than real wood while the manufacturing process utilizes recycled/excess materials thereby saving trees.
MDF is also excellent at resisting seasonal movements caused by heat and moisture, both of which plague real wood. It also machines very well.
On the flip side of the coin, MDF also suffers from several drawbacks. MDF is hard to repair once dinged or nicked up, due to its composition. MDF also doesn’t take nails very well, with the nails often ‘exploding’ out of the opposite side (much like laminates do). While MDF is resistant to normal fluctuations of humidity, direct contact with water will cause MDF to swell, as the open end-grain fibers will soak up water quickly, likely ruining that piece of the board.
Health Concerns for Woodworkers
One of the main concerns which has been raised surrounding the use of MDF focuses on the resins used in its manufacture. Cutting MDF releases micrometer-sized wood particles that irritate the eyes and upper respiratory tract. The same thing happens while cutting other wood products, especially plywood products, but it is especially bad with MDF, because of the product being made of separated wood fibers to start with. This leads to a finer dust being produced by the material when it is cut.
But it’s the formaldehyde which is contained in the bonding resins that’s the real concern. While the formaldehyde from both formaldehyde and urea-formaldehyde (UF) resin binders is known to irritate the eyes and upper respiratory tract, the most significant health concern associated with these binders is their potential as a carcinogen. Even so, a definitive link between these resins and cancer has not been established, it is merely suspect. The Material Safety Data Sheets (MSDS) for both resins only list them as ‘potential’ carcinogens or ‘suspected’ of causing cancer. The UF MSDS even went further and stated the link was ‘based on limited evidence.’
People who are calling these adhesives carcinogens are also calling wood dust a carcinogen. They are going so far as to call MDF “the new asbestos” because of the perceived danger. This is nothing more than fear-mongering, as with the formaldehyde, this has not been proven, although the fact that wood fiber dust is irritating to the upper respiratory system does make it a potential carcinogen; but that is only in its loose, airborne form.
This perceived health hazard is easily avoided with the use of proper personal protective equipment, specifically dust masks or respirators. In addition, adequate ventilation and dust control systems should be installed in the work area. Eliminating as much dust as possible from the environment reduces not only the potential risk of cancer, but also of other respiratory illnesses that can be caused by working in a dust-filled atmosphere. Those who work with MDF should follow any/all prudent safety precautions when handling MDF.
Please note that this risk is higher for those working in furniture or other wood factory settings, where they are exposed to airborne wood fiber dust from MDF and other wood products all day, every day. While there is no way to eliminate risk altogether, adhering to straightforward, standard safety precautions should allow people to work with (and discover the many wonderful benefits of) MDF as a building material without a fear of taking an unnecessary health risk.
Health Concerns for Homeowners
While the same sort of health concerns are being raised for homeowners, this is largely an unfounded concern. The risk of wood fiber dust shouldn’t exist with finished homes or wood furniture. The only time such risk can exist, would be during a remodeling project, where the homeowner is in the home, while the construction crew is working. In that case, the homeowner should take the same precautions with PPE that workers do.
While it is not clearly the contractor’s responsibility to provide this PPE for the customer, it is advisable to reduce your legal liability. At an absolute minimum, it would be a good idea to inform the homeowner of this risk, suggesting that they buy dust masks to wear while the work is in process.
The other part of the risk, that of the formaldehyde, is only in part associated with the wood dust. Due to the way that MDF is manufactured, wood dust will also contain adhesive dust, which means containing formaldehyde. Breathing in this dust can cause additional irritation, with the risk of respiratory problems.
Once the work is done and the worksite is cleaned up, the risk of breathing in formaldehyde in the dust is eliminated. However, the risk of outgassing of formaldehyde has been brought up as a further concern. It is unsure, at this time, whether there is any potential for outgassing of formaldehyde from the cured resins used in the manufacture of MDF.
Projects made from MDF can be made theoretically safer by painting or otherwise sealing the surfaces, especially the edges, which are more porous. If finishes are properly applied, filling all the pores in the wood product, this should capture any formaldehyde, preventing any that outgases from escaping into the home’s atmosphere. While this is not practical for some remodeling projects, it is very practical for the manufacture of furniture and other small projects where MDF is used. You may want to do this on any of your own projects, where you use MDF.
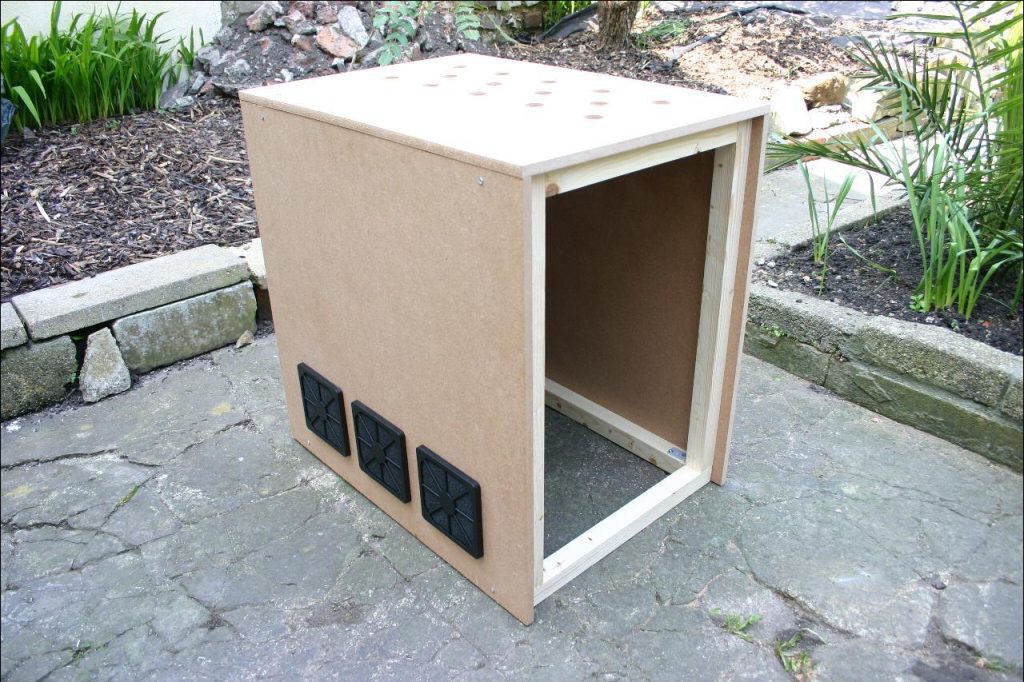
One Final Note
The safety concerns about MDF are not happening in a vacuum, where there is nobody paying attention to them. Government agencies in a number of countries, like the FDA in the United States, have taken note of the fact that formaldehyde is used in the manufacture of MDF, as well as a large number of other architectural products.
Limits already exist for the amount of free formaldehyde that can exist in the atmosphere, whether from outgassing or other more-natural processes. Those levels have actually been tightened up since the time when MDF first started being used commercially. The permissible levels which now exist are low enough so as to be a safe living environment, which should not cause cancer.