Owning a recreational vehicle can bring a lot of joy and enjoyment. At the same time, there can be a lot of work. Someone once said that a boat is a hole in the water that you pour money into, and an RV can be the land version of that saying, especially if you buy an older unit that needs a lot of work. Of course, doing that work yourself can save a lot of money, so don’t be dissuaded by that older unit. Someone who can do that work can turn that 30 or 40-year-old motorhome into a traveling luxury palace for a very reasonable price.
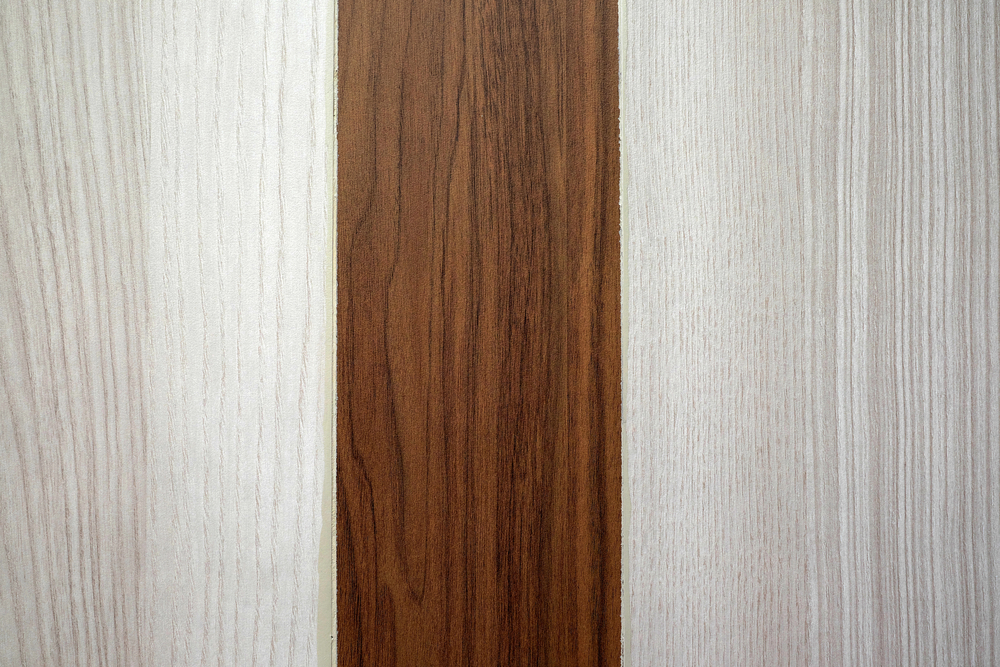
The most common problem with RVs is leaky roofs and the problems those roof leaks can cause. When water from the roof invades the thinly paneled walls, it doesn’t take long for the damage to begin. Often, that damage isn’t seen until it is rather severe because of the time an RV can spend parked, just waiting until the next time it is used.
As the water soaks into the paneling, it causes delamination, which is not made with an exterior-grade adhesive. As the wood delaminates, bacteria start working on it, decomposing it. This usually isn’t found until visible areas become damaged, but under further investigation, a larger hidden damaged area is encountered.
RV paneling is thinner than home paneling, usually only 1/8 inch thick. Like most paneling, it is a three-ply plywood product consisting of a thicker core with two veneer faces. In most cases, the face layers are not hardwood, as they are usually covered with wallpaper, often before they are installed. While there are thicker versions of this paneling, measuring in at 3/16” and 1/4”, those are not as commonly used.
This paneling isn’t available at most lumberyards and home improvement centers. You have to go to an RV repair or supply center, and even then, you might have to special order it. Finding an exact match may be difficult, especially matching the wallpaper. It is often necessary to redo the wallpaper on the entire wall or room, to finish out a repair.
How RVs are Built
Before repairing RV paneling, it helps to understand how it is built. This has changed over time, so we’ll have to look at two different methods. All RV walls are thin, usually measuring no more than 1 ¼” in total thickness and sometimes only 1 inch.
All RVs start with some chassis. In the case of trailers, the RV manufacturer usually makes the chassis using commercially available axles and other running gear. The structure sits on two main frame rails, spaced roughly one-third of the RV’s width apart, with crossbars going out to the outer walls. The subfloor and floor covering is installed on this, often before the walls are attached.
The interior walls of RVs normally aren’t designed to provide structural support for the roof. They may do so incidentally if the roof sags sufficiently to put pressure on them, but it is just as likely that the sag will cause the interior wall to buckle rather than provide support.
Older RV Construction
Older RVs and those made by smaller manufacturers are stick-built, much like framing a home. The exterior frame for the walls and roof is built onto the chassis out of individual pieces of square aluminum tubing and aluminum C-channel riveted together. Interior framing is usually 1”x 2” furring strips. There might also be some wood strips in the exterior walls, providing something to nail the paneling to.
The outer aluminum skin of these units is usually riveted to the structure, although it might be bonded with adhesives. One-inch-thick Styrofoam sheeting is typically used for the insulation, and the inside is either glued to the structure or brad-nailed in cases where wood is used in the structure.
The roofs on these older units are usually flat, with rectangular tubing spanning the full width. This can lead to sagging, either from the weight of the air conditioner or from the weight of storage pods on the roof. Sagging roofs are a major cause of leaks, especially around the air conditioner.
Newer RV Construction
Many RV manufacturers, especially the larger manufacturers, have switched from the abovementioned construction technique to making their walls and roofs as one-piece laminated constructions and then assembling them together to make the RV shell.
Usually, these walls are made with fiberglass skin, which is laid up first. Before the resin cures, the framework is laid in place, with the aluminum pieces riveted together. Then, once the rosin for the fiberglass cures, the expanding urethane insulation is sprayed in, and the interior paneling is set in place. The whole thing is held together in a low-pressure press until the expanding foam insulation has had time to cure. This insulation also acts as an adhesive to hold the entire thing together.
First Step
The first step in repairing any damaged RV paneling is ensuring the roof leak is solved. Roof leaks on RVs can be extremely hard to locate because the water seeping in through whatever hole in the roof can travel some distance inside the roof before coming out. At both points, the entry and the exit, that water is going to need a hole to go through.
When looking for a roof leak, check all the seams, vents, the air conditioning unit, and anything else that pierces the roof. Even the seemingly smallest hole, plugged by a screw, can cause a leak if it is not sealed properly. I had a serious leak in a motorhome roof caused by a hole underneath a bracket for the railing around the back end of the roof. It came from the factory that way and was invisible until the railing was removed. Yet the leak caused considerable damage to the inside of the motorhome.
If the leak isn’t apparent, it can be helpful to wet down the roof, especially on older RVs with sagging roofs. Wetting it down will help identify areas where water puddles, allowing for a more focused investigation.
Does the Paneling Need Replacement or Not?
Before rushing to replace the paneling on an RV, decide if it is really necessary. Paneling behind the oven or covering the walls inside of cabinets doesn’t necessarily need to be replaced. The rotted part of the paneling can be removed, leaving whatever remains. As long as the leak is stopped, any damaged insulation can be replaced using spray-in urethane foam insulation, and the area can be painted.
If the damage is bad enough in one of these hidden areas that it needs to be covered, one option, which does not require replacing the paneling, is to cover the damaged area with a door skin. These can often be purchased at RV repair supply houses. While a patch of this type may be a bit obvious, if it is inside a cabinet and the patch is cut to the full size of the cabinet, it may not be noticed.
Replacing RV Paneling
If visible paneling needs to be replaced, it can be. However, the process is a bit more complicated than replacing paneling in a home due to the furnishings in the RV and the way the paneling is bonded to the structure.
Start by removing everything attached to the wall: cabinets, furnishings, pictures, and anything else on there. If there is a window or door in the part of the wall where you are replacing the paneling, you’ll need to remove those, too. If your RV has trim on the floor and ceiling, try to pry it off without damaging it. Most likely, it will be installed with brad nails.
With everything removed from the wall, it’s time to remove the existing paneling. This will be difficult, as the paneling is stuck to the framework with some sort of adhesive.
It is usually best to work from whatever rotted area outwards, as that will probably give you an edge that you can slip something under to try and separate the existing paneling from the structure and insulation. Large putty knives are normally used for this, but a Japanese pull saw, like a Ryoba, works even better. Cut the paneling into sections, pry them off, and then scrape the remaining wood fibers and glue off the structural members.
Most adhesives will soften when heated, so using a heat gun or blow dryer can be useful in getting the glue off the structural members. For the best possible bond and to prevent waviness from having globs of glue and wood fiber on the structure, it is best to get as much of the glue off as possible. The heat gun may damage the insulation, but that can be replaced.
While scraping, remove the putty acting as a sealant under the window or door frame. This must be replaced with a new sealing putty, which can be purchased at an RV repair parts house.
Cut the individual pieces of paneling to fit. In cases where difficult contours may need to be cut or where it might be difficult to fit the pieces in place, it can be useful to make a pattern out of cardboard first, ensuring that it will fit and then transferring that contour to the paneling for cutting. Don’t bother cutting out window and door openings, as those can better be cut once the paneling is installed. Ensure that all edges of the new pieces of paneling land on a structural support element.
Because of the thin face veneer on the paneling, it is a good idea to stick masking tape to the surface while cutting and cutting from the pane’s back side. These measures will help reduce splintering caused by the blade’s side rubbing on the cut edge.
Before installing the new paneling, the insulation needs to be installed. There are three ways to go about this:
- Cut sheets of 1” Styrofoam insulation, available at any building materials center, and glue them in place.
- Cut fiberglass batts of insulation and glue them in place. If you can’t find R-5 batts, you may need to buy thicker batts and cut them down. Be sure to wear gloves when handling them.
- Use expanding urethane foam, often sold for gap filling. To do this, a scrap plywood covered with waxed paper should act as a mold. The insulation should be done in sections the size of the scrap plywood. Once dry, any excess protruding out can be cut off.
With the insulation in place, it’s time to install the new paneling. It needs to be installed with some adhesive. The best is a relatively slow-drying two-part epoxy (30 min. to 1 hr.). Construction adhesives can also be used, but it will be more difficult to compress the adhesive enough so the paneling is right up against the structural element. Silicone caulking can also be used, as it is a good, flexible adhesive.
Before applying the glue, test fit the part and dry clamp it in place to ensure that there are enough clamps and that the clamps won’t leave any points loose. In many cases, it will be better to put a 2”x 4” or other board up against the paneling and clamp it to the wall, allowing the clamp to cover a wider area.
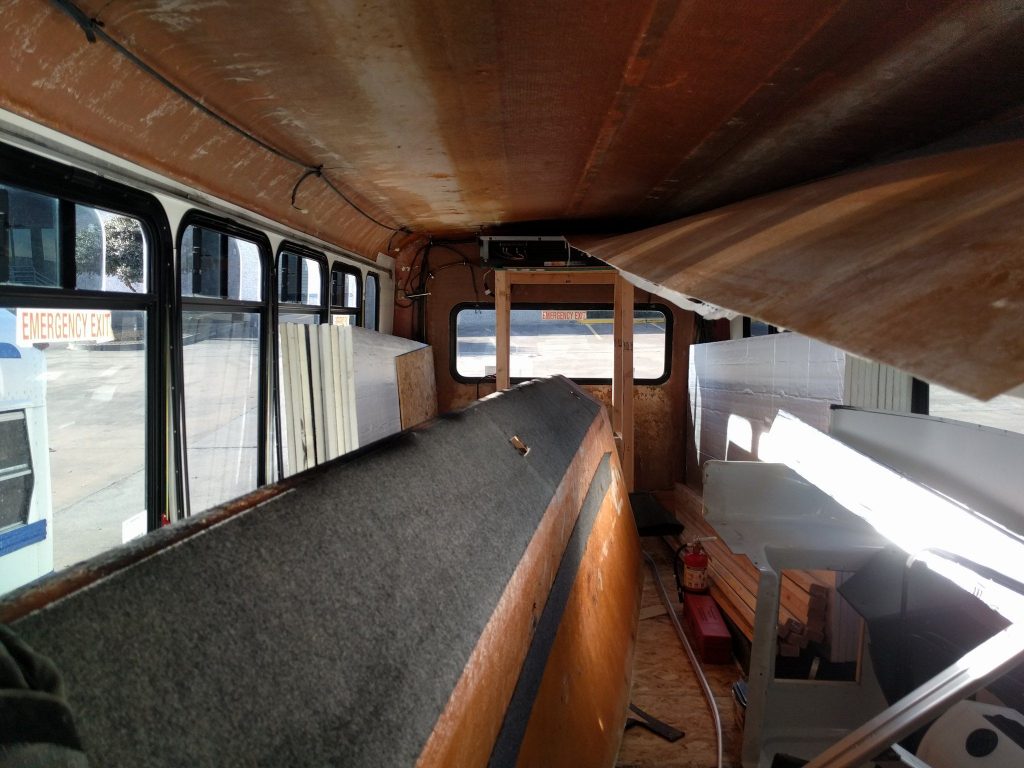
Apply the glue, set the panel in place, and clamp it, leaving it there long enough to ensure the adhesive has fully cured or dried.
With the clamps removed, window and door openings can easily be cut out with a jigsaw, using the outer skin as a template. Take care not to overcut, as it will require repairing the outer skin. Reinstall trim, windows, and any furnishings removed to make the repair.
Other Options to Consider
The process of replacing paneling in RVs is rather difficult and time-consuming, although it doesn’t require any extraordinary skills or tools that the average handyman doesn’t have. However, it is easy to see why many would want to avoid the project, seeking an easier way to repair their RV’s walls.
To save work, new material can be overlaid on the damaged paneling. This can be new paneling or:
- Tongue & groove wall planks
- Tongue & groove wood flooring
- Textured aluminum or stainless steel
- Upholstery fabric
- Kydex plastic (commonly used for interior trim pieces on buses and airplanes)
- Fiberglass panels
- Ceramic wall tile (not highly recommended)
Anything you can mount to a wall in a home can be mounted on the interior walls of your RV. The one thing you want to consider is the weight. RVs are heavy enough as they are, and they aren’t designed to add a lot of additional weight. So, when it comes to materials like stainless steel and ceramic tile, they’re fine for small areas but might not be good for larger areas.
The other consideration is flexibility. The walls of an RV will flex somewhat as the vehicle goes down the road. That makes it extremely difficult to keep ceramic wall tile and other materials that do not flex on the wall. Materials with some flexibility, attached with adhesives that also have some flexibility, are the best option.
Use adhesive across the entire repair surface area as much as possible rather than just gluing the perimeter and an X on the back of the wall covering. While a smaller amount of adhesive may work, it is also much more susceptible to cracking due to flexing, as there will be edges of the adhesive where the cracking can occur.