The thickness of plywood is used for different purposes. Plywood refers to a whole family of engineered wood products produced in panels. While various hardwood products fall into this definition, not all of them fit the description of traditional plywood. However, each fulfills a specific purpose for their designed outdoor applications.
Different types of plywood are produced in a range of thicknesses from 1/8″ to 1-1/4″ thick. However, not all types of plywood manufactured here are available in the various thicknesses being manufactured. A lot depends on what the specific type of plywood or product has been designed to be used for. This chart gives you an idea of the standard thicknesses of the most common types of plywood manufactured here:
Plywood Thickness: | 1/8″ | 1/4″ | 5/16″ | 3/8″ | 7/16″ | 1/2″ | 5/8″ | 3/4″ | 1-1/8″ | 1-1/4″ |
---|---|---|---|---|---|---|---|---|---|---|
Softwood Plywood | ![]() | ![]() | ![]() | ![]() | ![]() | ![]() | ||||
Hardwood Plywood | ![]() | ![]() | ![]() | ![]() | ||||||
Luan Plywood | ![]() | ![]() | ![]() | ![]() | ||||||
Marine Plywood | ![]() | ![]() | ![]() | ![]() | ![]() | ![]() | ![]() | |||
Particle Board | ![]() | ![]() | ![]() | |||||||
MDF | ![]() | ![]() | ![]() | ![]() | ![]() | ![]() | ![]() | ![]() | ||
MDO | ![]() | ![]() | ![]() | ![]() | ||||||
OSB * | ![]() | ![]() | ![]() | ![]() | ![]() | ![]() | ![]() | |||
ApplePly * | ![]() | ![]() | ![]() | ![]() | ![]() | ![]() | ![]() |
|||
Baltic Birch ** | ![]() | ![]() | ![]() | ![]() | ![]() | ![]() |
Notes for this chart:
* Also available in additional thicknesses.
** Please note that Baltic Birch is produced to metric dimensions. The dimensions here are approximate equivalents.
Plywood thick 3/4″is the widest of utility plywood sizes, sold in sheets in most lumberyards and home improvement centers. Utility plywood is commonly manufactured in 1″ hardwood and 1 ¼” thick plywood sizes, too. Some mills produce some plywood sizes up to 3″ thick for special orders. These thicker plywood products are typically used in specialized furniture making, such as tops for industrial workbenches.
Sheets
Most plywood products are commonly available in standard plywood sizes of 4′ x 8′ sheets, regardless of thickness. Baltic Birch is more commonly available in 5′ x 5′ plywood sheets now, the standard European size for plywood sheets. Even so, manufacturers of Baltic Birch, like those of other plywood products currently manufactured in Europe, are gradually switching to the American standard plywood sizes of 4’x 8′ plywood sheets again.
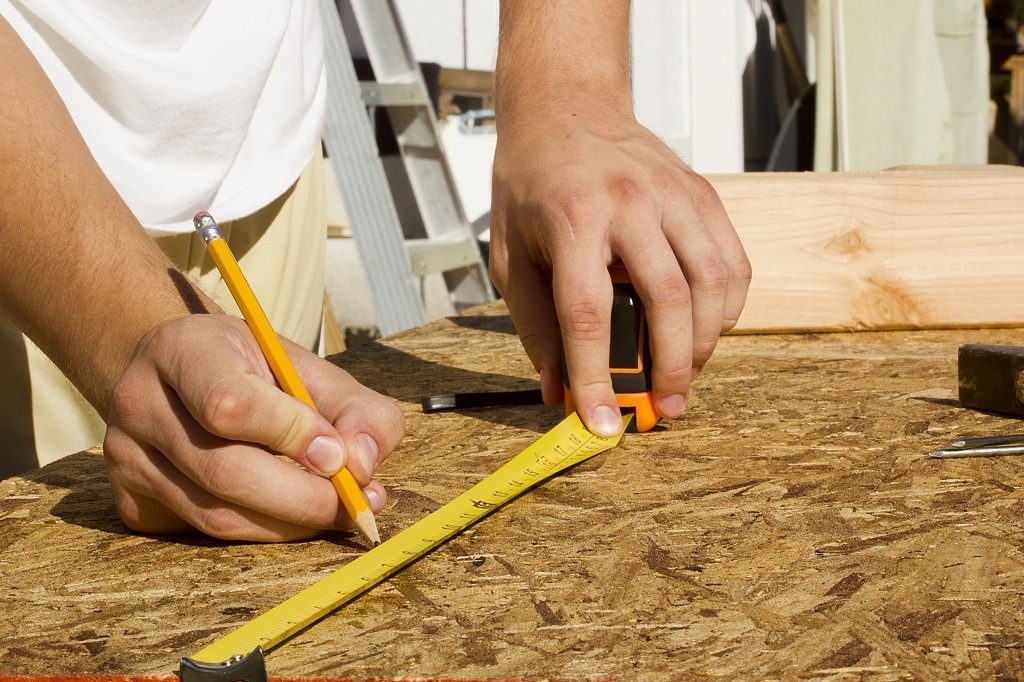
Carpenter Measuring OSB
Baltic Birch is not the only plywood product manufactured in 5′ x 5′ sheets. Many hardwood plywood products are also produced in this size, especially when manufactured in Europe, for the European market. Although the 4′ x 8′ standard sheet size is the most common, some types of marine-grade plywood are produced in 4′ x 10′ and 4′ x 12′ sheets for industrial applications. For example, OSB is manufactured in sheets up to 24′ long. The enormous sheets of any marine grade plywood are 6000mm x 2200mm (19’-8-1/4″ x 7’-2-5/8″). However, any marine-grade sheet of plywood in larger sizes would typically only be available by particular order.
Generally, a 4’x 8′ sheet of plywood will measure exactly 48″ wide and 96″ long. It is rare to find it off by more than 1/32,” or so. Mills cut the plywood to exacting dimensions because it is necessary for the construction of homes and other buildings. If sheets were only 1/8″ long or wide, subflooring would be off the edge of floor joists, wall studs or rafters in six sheets. The only way to prevent that would be for carpenters to finish cutting every panel before installing it, an expensive undertaking.
Some retailers also offer thin plywood project panels, especially for hardwood plywood cabinets, smaller than full sheets of thicker plywood. While 2’x 4′, 2’x 2′, and 4’x 4′ are the most common sizes for these, a variety of other sizes are available, specialty sizes such as 10″ x 30″. These retailers are trying to meet the needs of their customer base, marketing panels that fit common project plans.
The nominal and actual thickness
We need to keep two very different thicknesses and definitions in mind when discussing plywood; that nominal and actual plywood have different thicknesses. Like dimensional lumber, most plywood is rated at a nominal thickness; the thickness before it is sanded. The actual thickness is just like it sounds – the thickness of the plywood panels you buy after sanding. Typically, the actual thickness of plywood panels is 1/32 inch less than the nominal thickness.
Part of the reason for this difference is industrial manufacturing, where thin plywood often is used in product design. Industrial machinery handles the wood grain, and machines plywood for furniture and cabinetry can handle wood grain in slightly thinner material without a problem. But when that material is thicker than nominal, it is a problem for those operations, especially joining parts together.
Rather than being concerned that the plywood is too medium-density fiberboard too thin. We should remember that dimension of lumber core plywood is considerably smaller than its nominal dimension. By comparison, a 1″ x 4″ particle board is 3/4″ x 3-1/2″, a full 1/4″ thinner and 1/2″ narrower than the nominal dimension lumber core plywood. That makes the 1/32″ difference in plywood’s nominal length and plywood measures actual thickness seem much more trivial.
The table represents the comparison between nominal hardwood plywood grades and actual softwood plywood grades and thicknesses:
Nominal Thickness | Actual Thickness |
---|---|
1/4” | 1/4” |
3/8” | 11/32” |
1/2” | 15/32” |
5/8” | 19/32” |
3/4” | 23/32” |
1-1/8” | 1-1/8” |
Most lumberyards have switched to listing the actual plywood thicknesses and sizes on their racks in the exact thickness rather than the nominal thickness. However, it can be a head-scratcher when you’re standing there looking at it and deciding what standard sizes, plywood thickness, and length you need to buy.
The trick here is understanding what a half inch is in that thickness. Since they are listing it in the 32nds of an inch, we need something that is about half of that, or 16/32. What we have is 15/32″. If you can remember that one thickness, you’ve got it made. To get 3/4″, all you do is add a half of 15 to the 15 that’s above the line, which means you want something that’s about 22/32″. As you see in the chart above, we’ve got 23/32″; so that next layer has to be the 3/4″ equivalent. The other thicknesses fit between these two, making it easy to see what they are.
Please note that even the “actual sheet thickness” isn’t a perfect dimension but an approximation. If you were to measure the exact thickness of that sheet with a pair of dial calipers (or digital calipers), you would find that it isn’t that thick. Instead, it will vary slightly due to the manufacturing process.
This variation is consistent in any plywood bunk, as the whole bunk comes from the same mill and is made simultaneously. What makes the variation exist isn’t the laminating process but the sanding process. Settings on the machine and wear on the sanding belt can easily cause those slight variations. To prevent them from causing a problem on a project, buying all the proper plywood and the correct sheet of plywood in the same place simultaneously is best.
Moisture can affect the thickness of the veneer core plywood products as well. When the finished surface of the veneer core plywood is manufactured, there is a certain amount of water in the wood veneers. The veneer core plywood sheets will become slightly thinner as that sheet dries further. Should thin veneers of wood bonded to the sheet be left in a high moisture environment, they will gradually become slightly thicker again.
This change in the thickness of thin layers on the plywood can work to pull nails loose, not all the way loose, but enough to be noticeable. Using screws or adhesives to hold the thin layers and types of plywood and parts together on a plywood project will eliminate the risk of glue on the fasteners loosening up from absorbing moisture and drying cycles.
Thickness in millimeters
Although plywood measures made in inches are the most common, some other plywood thicknesses are expressed in millimeters, especially for European plywood products. The best example is Baltic Birch plywood (sometimes called Russian or Finland Birch). Another plywood product typically sold in metric thicknesses is aircraft plywood, a product common during World War II but not so common today.
Thickness (inch) | Thickness (milimeter) |
---|---|
1/8” | 3.2mm |
1/4” | 6.4mm |
5/16” | 8mm |
3/8” | 9.5mm |
7/16” | 11.1mm |
1/2” | 12.7mm |
5/8” | 15.9mm |
3/4” | 19mm |
1-1/8” | 28.6mm |
1-1/4” | 31.75mm |
When selecting, you want to avoid misunderstanding the thicknesses of any plywood product you buy. You can best avoid those misunderstandings by looking at and understanding the dimension comparisons between these two standard units of measure. Also, be careful and keep it in mind when comparing the prices.
Selecting plywood thickness
In many cases, selecting a particular type of plywood and thickness is based more on the convenience of using that actual thickness for different purposes and thickness for the work being done than anything else. Plywood is strong enough to provide more strength and stiffness than is needed in a particular application.
Nevertheless, there are applications where the strength and stiffness of the plywood is the determining factor in selecting a particular thickness of plywood for different purposes and thickness. Such is the case for plywood structural elements used in building homes. The same can apply to many other applications, such as making furniture and shipping crates.
There are several factors associated with the thickness of the plywood sheet and how it is installed, which affect the strength and stiffness of a particular type right thickness of plywood sheet:
- Thickness – obviously, the thicker the plywood sheet, the stronger and stiffer it is
- Number of Plys – the more individual layers the sheet of plywood has, the stronger and stiffer it is
- Support Span – the farther apart that supporting elements are spaced, the more of a chance for the plywood to flex
- Direction – plywood is stronger along the “strength axis,” which is the axis parallel to the face veneer. That is because it has one more ply with the grain running in that direction
The most obvious of these factors is the thickness of the plywood. Just how strong plywood is made is a bit hard to understand. While the various types of plywood have been tested over the gambit of support options encountered in most building materials, the resulting data is not presented in a manner the layperson might understand. Part of this is because of the wide variety of support options used in construction and how much that support affects the strength of any structure built out of plywood.
Nevertheless, we can gain some insight into the strength of different grades and thicknesses of plywood flooring by looking at the requirements in the building code. Floors that support at least 50 pounds per square foot are built out of 3/4″ thick softwood plywood or OSB. While that 50 lbs. may not seem like much, we must consider that over-floor joists can be as much as 24 inches apart. So we’re talking 100 pounds between any two-floor joists. At that span, the problem is flexion more than anything else. While the same type of plywood flooring could support more, you’d probably feel uncomfortable walking on it.
Roofs can be sheathed with wood
Roofs, which can be sheathed with wood or 3/8″ thick softwood plywood, in most jurisdictions, are designed to carry a load of 20 pounds per square foot. Once again, the two layers of wood rafters are allowed to be 24″ apart. In perspective, 10 inches of fresh snow weighs about five pounds per square foot. So a roof of 3/8″ softwood plywood, over 2″ x 6″ with wood rafters spaced every 24″, can support 40 inches of snow.
Please note that this is “freshly fallen snow.” Snow tends to pack down as it accumulates, so if you have snowstorms sufficiently close together that the snow from one hasn’t melted before the next snowfall, the overall weight will be more than 5 lbs. per square foot for the total accumulation. Therefore, areas of the country with high snow accumulations may require that roof sheathing be 1/2″ softwood plywood as a safety precaution, increasing the dead snow load up to 30 lbs. per square foot.
Plywood for construction
Softwood plywood is commonly used in the construction of homes and other buildings. Since houses are typically wood-framed, the average home has a considerable amount of plywood. This plywood is used for roof sheathing, wall sheathing, and subflooring. The thicknesses of plywood most often found used in home construction are 3/8″, 1/2″, and 3/4″.
Actual thicknesses and types of plywood and products used right plywood in home construction depend on the building code used in that municipality. While most cities use the Uniform Building Code (UBC) or the International Building Code (IBC), some cities have adopted state or local building codes. Of these two standards, the UBC is older and has, for a large part, been replaced by the IBC.
While it’s easy to say that local building codes are nothing more than bureaucracy run wild, the truth is that some jurisdictions have determined that the requirements in the UBC or IBC are inadequate to their residents’ needs, usually due to weather considerations. Roof load requirements for a home built in Alaska, where they get much more snow, are a much bigger issue than for Florida. Therefore, the building code in Alaska may be modified, requiring thicker sheathing and stronger rafters.
Leaving that aside, the following standard thicknesses can be expected. However, you should check on the requirements where you live before starting any construction project to ensure that building materials for your next home improvement project will pass inspection.
- Roof sheathing – 3/8” or 1/2” CDX softwood plywood
- Wall sheathing – ½” CDX softwood plywood. However, this is only required in the corners of the building. The rest of the sheathing can be Styrofoam insulation
- Subflooring – 3/4″ softwood plywood or OSB
7/8″ plywood subflooring
As construction techniques have changed, so have the materials used to construct homes. One such material change is the spacing increase for floor joists from 16″ centers to 24″ centers. While this meets the technical requirements of the IBC, it produces a floor that is more susceptible to flexing, creating squeaks and a “spongy” feeling when walking on it.
This can be even more of a problem for homes built with ceramic tile or solid wood flooring. These types of flooring need a solid subfloor, which will not flex. Flexing the subfloor under ceramic solid wood tile can cause the mastic to come loose from the tile, the grout to break out from between tiles, and the tiles themselves to break. In such cases, the solution is to upgrade the 3/4″ nominal subfloor to a 7/8″ subflooring (actual dimension). The thicker 7/8″ subfloor provides double the 23/32″ OSB subflooring stiffness.
This is a more cost-effective solution than putting in a double layer or three layers of 3/4″ plywood subflooring, done during remodeling projects where ceramic tile floors are to be installed over.